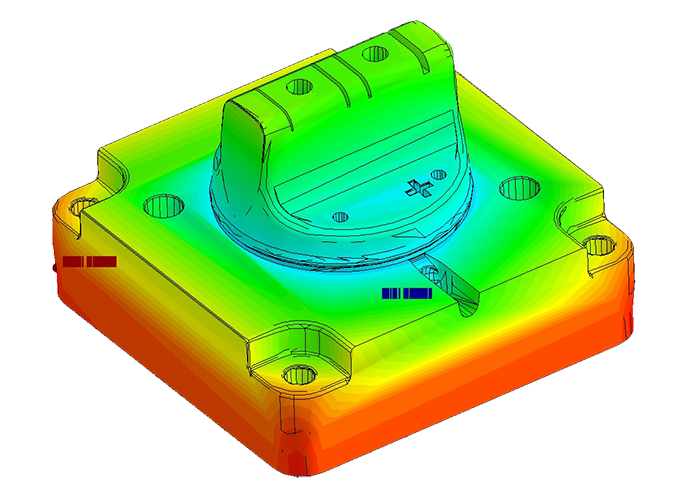
3D-gedruckte Einsätze
Simulationssoftware für die Additive Fertigung von Werkzeugeinsätzen
SimpaTec hat sich mit Simulationssoftware für den Spritzguss einen Namen gemacht.
Das Softwaretool MSC.Digimat-AM nutzt die Ergebnisse der Spritzgießsimulation für die Fertigung von 3D-gedruckten Werkzeugeinsätzen.
Um bei 3D-gedruckten Werkzeugeinsätzen eine hohe Flexibilität im Design, die schnelle Fertigung sowie geringe Kosten gewährleisten zu können, werden vorangehende Analysen für eine sichere Auslegung benötigt. Mit MSC.Digimat-AM stellt die SimpaTec die erste Prozesssimulation für Kunststoffbauteile im Bereich der Additiven Fertigung vor. Dabei können verschiedene Additive Prozesse sowie unterschiedliche Materialien, wie z. B. verstärkte Composites, in der Simulation abgebildet werden. Mithilfe der Analyse der Prozesssimulation werden virtuell die Thematiken der Eigenspannungen, der Schwindung und des Verzugs dargestellt und deren Optimierung ermöglicht. Durch numerische Berechnung kann der Werkzeugeinsatz im Vorfeld maßhaltig an das Werkzeug angepasst werden.
Die Spritzgießsimulation umfasst nach heutigem Standard die Modellierung sowie Berücksichtigung von Werkzeugeinsätzen. Dabei spielt zum einen die Temperierung des Einsatzes und zum anderen die mechanische Beanspruchung während des Spritzgießprozesses eine maßgebliche Rolle. Mittels experimenteller Datensätze erfolgt das Fitten der Materialmodelle für die rheologischen und mechanischen Materialeigenschaften.
Weitere Module in der Spritzgießsimulation berücksichtigen die Wechselwirkung zwischen dem anliegenden Druck der Schmelze und der Deformation des Werkzeugeinsatzes. Hierdurch sind direkte Aussagen über das lineare mechanische Verhalten der Werkzeugeinsätze möglich. Um die Aspekte der Mikrostruktur eines 3D-gedruckten Werkzeugeinsatzes in die strukturmechanische Finite-Elemente-Analyse (FEA) einfließen zu lassen, erfolgt eine Kopplung mit einem mikromechanischen Softwaretool und einem gängigen Finite-Elemente-Solver.
Viele Parameter ergeben ein Gesamtbild
Um verlässliche Aussagen zum Bauteilverhalten von 3D-gedruckten Bauteilen zu erhalten, muss der jeweilige Herstellungsprozess in einer gekoppelten Berechnung mit einbezogen werden. Die prozessinduzierten Eigenschaften definieren die lokale Mikrostruktur, wobei das Bauteil kein symmetrisches oder isotropes Verhalten, sondern ein komplexes anisotropes Verhalten über die Wandstärke und lokale Position aufzeigt. Beginnend mit dem gewählten Prozess der Additiven Fertigung findet eine Festlegung der prozessinduzierten Mikrostruktur statt. So existiert bei einem SLS-Verfahren (Selektives Laser Sintern) eine hohe Abhängigkeit der Festigkeit vom gewählten Druckwinkel. Beim FFFVerfahren (Fused Filament Fabrication) wiederum entstehen Einsparpotenziale beim Gewicht. Mit einem intelligenten Design des Spritzgießbauteils, des Angusssystems oder auch der Temperaturführung kann der während des Spritzgießprozesses wirkende Druck auf den Werkzeugeinsatz verringert werden.
Über die integrierten Exportschnittstellen wird z. B. die Weitergabe von Faserorientierungen, Drücken oder Temperaturen an die FEA gewährleistet.
Bei der Kopplung von Mikromechanik und nichtlinearer Strukturmechanik können sowohl die prozessinduzierten Eigenschaften als auch das komplexe nichtlineare Materialverhalten in der Analyse des Bauteilverhaltens berücksichtigt werden. Das komplexe Materialverhalten von Composites kann in mikromechanischen Softwaretools berechnet werden.
Darüber hinaus existiert die Möglichkeit, eine digitale Materialkarte an experimentelle Daten zu kalibrieren. Eine weitere Besonderheit stellt die Versagensmodellierung dar. Hierbei wird das Materialversagen in Abhängigkeit der jeweiligen Phase (Matrix/Verstärkungsstoff) oder des Orientierungswinkels modelliert. Auch die Modellierung von Porosität bei Verwendung eines FFF-Prozesses oder der Kombination mit einem Composite ist möglich. In den softwareeigenen Schnittstellentools lassen sich im Anschluss die Informationen aus dem Herstellungsprozess, der komplexen nichtlinearen Materialkarte mit dem strukturmechanischen Modell automatisiert koppeln. Ferner findet die Berechnung über den Solver und die Analyse im Post-Prozessor statt.
Schlussendlich soll der MSC.Digimat-AM eine gesamtheitliche Betrachtung von Herstellungsprozess, physikalischem Materialverhalten und Bauteilperformance ermöglichen. Die numerische Berechnung sorgt laut Hersteller dafür, stabile sowie robuste Prozesse für die Fertigung zu definieren sowie die wechselnseitige Abhängigkeit von Prozess, Materialverhalten und Bauteilverhalten aufzuzeigen.
Artikel erschienen in Form+Werkzeug 02/2020