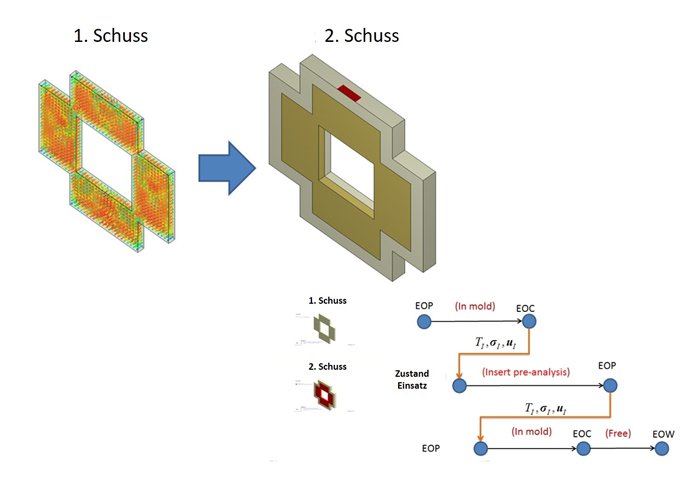
Mehrkomponenten-Simulation unter Berücksichtigung der Eigenschaften der ersten Komponente
SPEZIELL FÜR UNSERE ANWENDERSuchen Sie eine Möglichkeit, verschiedene Werkstoffe zu kombinieren, um unterschiedliche Eigenschaften (z.B. Haptik, Farbe, mechanisches Verhalten, …) gezielt in ihrem Bauteil zu vereinen? Dann ist die Mehrkomponenten-Spritzgießtechnologie ein bewährtes Verfahren. Lesen Sie in unserem Artikel wie Moldex3D die Eigenschaften der ersten Komponente im weiteren Prozess berücksichtigt.
Die Mehrkomponenten-Spritzgießtechnologie integriert zwei oder mehrere Kunststoffe effizient in einem Bauteil und ist in der Industrie weit verbreitet. CAE-Analysen ermöglichen, die Produktqualität im Voraus zu analysieren und damit entsprechende Maßnahmen zu ergreifen, um voraussichtliche Fertigungs- oder Bauteilprobleme frühzeitig zu erkennen und zu lösen. Wenn jedoch ausschließlich die Simulation der zweiten bzw. letzten Komponente berücksichtigt wird, ist eine akkurate Analyse der Produktqualität und Designoptimierung nicht gewährleistet. Die Eigenschaften der ersten Komponente am Ende des Prozesses beeinflusst das Ergebnis des nachfolgenden Prozesses aufgrund unterschiedlicher Eigenschaften wie Temperatur und Eigenspannungen. Daher besteht die Notwendigkeit, diese Effekte in der Simulation des nachfolgenden Prozesses zu berücksichtigen.
Die Frage, die zunächst gestellt werden muss, ist wie sich die Materialeigenschaften des ersten Spritzvorgangs auf der Bauteilkomponente des zweiten Prozesses wirken. Hier spielen die mechanischen und thermischen Ausdehnungseigenschaften der Materialien eine wichtige Rolle und beeinflussen direkt das Verzugsverhalten des Endergebnisses. In dem Mehrkomponentenverfahren kann das Endprodukt aus mehr als zwei Materialien zusammengesetzt sein und ohne eine Kopplung der Zwischenzustände der jeweilige Spritzgussvorgänge in der Simulation, ist eine aussagekräftige Analyse nicht möglich. Wenn eine Bauteilkomponente aus faserverstärktem Kunststoff besteht, beeinflussen dessen anisotrope Eigenschaften ebenfalls die Verformung des Endprodukts. Somit besteht hier auch ein direkter Einfluss der Faserorientierung auf das gesamte Kunststoff-Bauteil.
Die Werkzeugkonstruktions- und Verarbeitungsbedingungen leiten sich von den internen Druck- und Temperaturzuständen der ersten Komponente ab. Aufgrund der Wechselwirkungen zwischen den verschiedenen Komponenten führt der Ausgangszustand der ersten Komponente (Einlegeteil) zu Veränderungen in der Wärmeleitung und im Spannungsausgleich des Gesamtproduktes. Um die Qualität des Endprodukts zu gewährleisten, müssen wir daher auch den Herstellungsprozess des vorherigen Schusses berücksichtigen
In Moldex3D werden alle Spritzgussvorgänge mit der jeweiligen Komponente simuliert. In jedem nachfolgenden Simulationsschritt werden das vorherige Spritzgussbauteil als Einlegeteil mit der nachfolgenden Komponentenkavität modelliert. Die Ergebnisse der Füll-, Nachdruck- und Kühlphase inklusive die Faserorientierung des vorherigen Prozesssimulation werden hierfür mit in die Simulation einbezogen. Somit berücksichtigt Moldex3D die Kopplung der verschiedenen Effekte und Zustände, einschließlich der Temperatur und Eigenspannungen des vorherigen gespritzten Bauteils. Zusätzlich sind Effekte wie das Wiederaufschmelzen vorheriger Komponenten darstellbar.
Interessiert?!
Bitte wenden Sie sich an: 0241 565 276-0 oder senden Sie eine Email an info@simpatec.com .