Warum „Familienwerte“ für ähnliche, faserverstärkte Kunststoffe die einzelnen Messungen der Compounds nicht ersetzen können. Ein Fallbeispiel aus der Moldex3D®-Datenbank.
Bei der Fülle an Verarbeitungsmethoden für Kunststoffschmelzen sind allgemeine Regeln schwierig zu finden. Um auf dem hart umkämpften Markt firmeneigenes Knowhow und Wettbewerbs-Vorsprung zu sichern, setzen Unternehmen oft auf Spezialverfahren, Modifikationen und clevere Prozess-Kombinationen. Auch die Hersteller von Compounds nutzen ihre speziellen Kenntnisse für die Herstellung einzigartiger, hochwertiger Materialien oder optimieren diese auf das beste Preis-Leistungs-Verhältnis. Bei der zeitgemäßen, digitalen Produktentwicklung durch CAE (computer aided enginneering) sind die digital abgebildeten Eigenschaften dieser Compounds ein erheblicher Wettbewerbsfaktor. Sie werden zu diesem Zweck im Labor bestimmt und in Materialdatenbanken und Simulations-Tools zur Verfügung gestellt. Bei der Urformung durch das Spritzgießen sind die Fließ- und Erstarrungseigenschaften von besonderer Bedeutung.
Das Fließen einer Thermoplastschmelze wird durch die dynamische Viskosität beschrieben. Sie ist abhängig von der wirkenden Schergeschwindigkeit. Je größer die Schergeschwindigkeit, desto niedriger ist die Viskosität der Schmelze – sie fließt also umso leichter, je schneller sie sich bewegt. Diese Eigenschaft wird bei jeder Charakterisierung eines Kunststoffs im Hochdruck-Kapillar-Rheometer (HKR) bestimmt und nach Anwendung notwendiger Korrekturfaktoren im doppelt logarithmischen Netz dargestellt. Die Form der Kurve ist für Thermoplaste charakteristisch und Bestandteil der Grundkenntnisse in der Kunststofftechnik. Abbildung 1 stellt diese beispielhaft für ein Polypropylen dar.
Fallstudie "Familienwerte"
Ähnlich und doch völlig verschieden
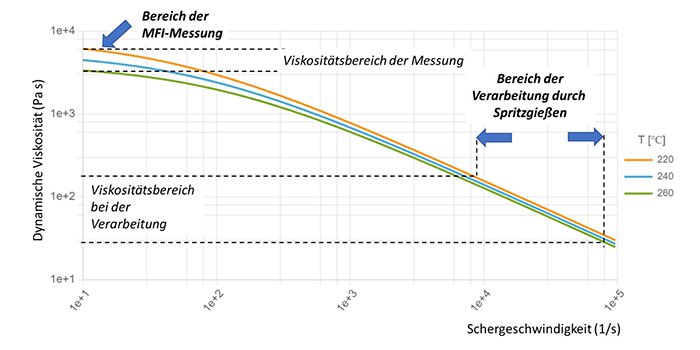
Abbildung 1: Scherviskosität eines Beispiel-Polypropylens bei drei Temperaturen und Schergeschwindigkeitsbereichen für MFI-Messung sowie Spritzgieß-Verarbeitung [1]
Die Darstellung verdeutlicht zudem, dass die Messung des Fließindexes (MFI oder MFR) ein Kennwert ist, der die, bei sehr langsamen Fließen, gemessene Viskosität beschreibt. Sie hat zumeist wenig mit dem Verhalten während der Verarbeitung zu tun. Die genaue Form der Viskositätskurve ist von Material zu Material unterschiedlich, das heißt ähnliche MFI-Werte führen nicht zwangsläufig zu ähnlichem Fließverhalten bei der Verarbeitung (siehe „Bereich der Verarbeitung beim Spritzgießen“). Werden Vergleichs- oder Alternativmaterialien benötigt, dann müssen auch die Viskositätskurven bei relevanten Verarbeitungsgeschwindigkeiten möglichst übereinstimmen.
Nicht nur Prozessparameter wie Druck, Temperatur und Geschwindigkeit, sondern alle Inhaltsstoffe einer Compound-Rezeptur wie Weichmacher und Füllstoffe sowie die Molekülmasse des Polymers beeinflussen die Viskosität. Die Kurve bleibt zwar in ihrer Scherabhängigkeit erhalten, aber wie bei der Temperaturänderung auch, wird sie durch die Modifikationen in einem bestimmten Bereich verschoben.
Nicht nur Prozessparameter wie Druck, Temperatur und Geschwindigkeit, sondern alle Inhaltsstoffe einer Compound-Rezeptur wie Weichmacher und Füllstoffe sowie die Molekülmasse des Polymers beeinflussen die Viskosität. Die Kurve bleibt zwar in ihrer Scherabhängigkeit erhalten, aber wie bei der Temperaturänderung auch, wird sie durch die Modifikationen in einem bestimmten Bereich verschoben.
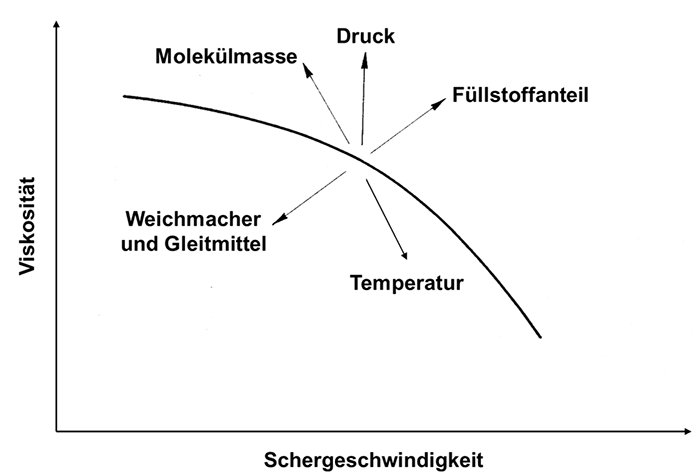
Abbildung 2: Grundsätzliche Einflüsse auf die Viskosität einer Thermoplast(-compound)schmelze [2]
Wird bei einem Compound ausschließlich der Anteil an funktionalen Füllstoffen wie Fasern oder Mineralien geändert und bleibt die Rezeptur ansonsten vollkommen gleich, dann folgt die Viskositätskurve innerhalb bestimmter Grenzen der beschriebenen Gesetzmäßigkeit mit steigendem Anteil an Beladung auch höher viskos zu fließen (siehe Abbildung 3, dargestellt bei kleinen Schergeschwindigkeiten und unterschiedlichen Füllgraden an Kaolin in Gewichtsprozent der Rezeptur).
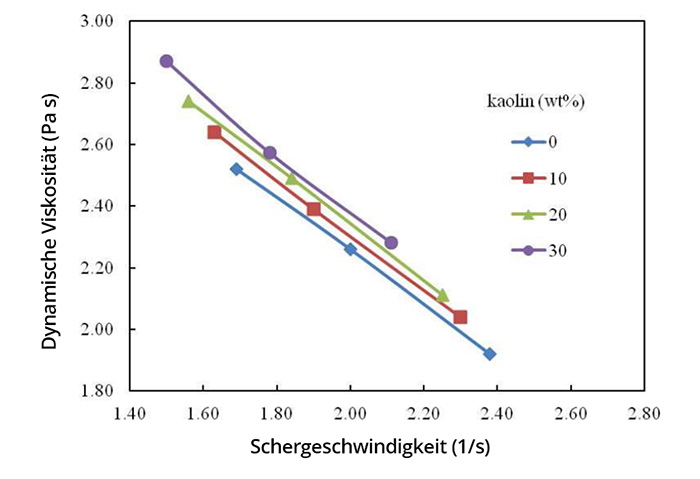
Abbildung 3: Viskosität in Abhängigkeit des Füllstoffgehalts an Kaolin bei ansonsten gleicher Rezeptur [3]
Für eine zeitgemäße Produkt- und Prozessentwicklung mittels CAE ist diese Materialcharakterisierung unerlässlich. Trotz der zahlreichen Vorteile und der hohen Verbreitung dieser Technologie wird sie jedoch oft vernachlässigt. Als Argumente werden die Vielzahl verfügbarer Materialien oder eine geringe Abnahmemenge genannt, bei der sich der zusätzliche Kostenaufwand angeblich nicht darstellen ließe. Sehr oft wird die Frage nach gewünschten Materialdaten auch mit „geeigneten, bereits in den Datenbanken existierenden Vergleichsmaterialien“ beantwortet – dieses Vorgehen zeigt, dass die Prozess-Simulation oft noch als Zusatzaufwand angesehen wird. Nachhaltig erfolgreiche Unternehmen beweisen hingegen schon seit Jahrzehnten, dass hohe Wertschöpfung und ein immenser Erkenntniszugewinn Ergebnisse klug angewandter Prozess-Simulationen sind.
Wird dieses Potenzial nicht erkannt, bleibt die Materialcharakterisierung zunächst hauptsächlich ein Kostenfaktor. Dabei stellt sich die Frage, ob sich aus einer Familie ähnlicher Rezepturen rein rechnerisch eine „Familien-Abhängigkeit“ ermittelt lässt, die diesen Kostenfaktor reduzieren würde. Nach dieser Vorstellung charakterisiert ein Hersteller von Compounds eine Rezeptur, mit zum Beispiel 20 % und 50 % Glasfasern, rheologisch und werkstofflich. Die Werte „dazwischen“ werden mehr oder weniger als linear annehmen und entsprechend abgeschätzt. Ähnliche Überlegungen am Markt fordern unter Verwendung der gleichen Argumente, den Einfluss von Masterbatches (hoch konzentrierten Farb- oder Additiv-Compounds) in einem Materialdatensatz zu berücksichtigen. Der Einfluss von Farben und Additiven solle nicht extra gemessen werden, sondern einfach durch Grundeigenschaften und Dosierung abgeschätzt werden.
Diese Forderung zur Reduzierung des Mess-Aufwands soll anhand der Viskositäten und des Erstarrungsverhaltens technischer Kunststoffe (PA66-Glasfasercompounds) mit unterschiedlichen Fasergehalten und verschiedener Hersteller bewertet werden. Hierfür werden vorhandene Messwerte ähnlicher technischer Compounds ausgesucht und in Vergleichsdiagramme überführt. Anhand der Fasergehalte werden die Fließ- und Erstarrungsdaten verglichen und bezüglich der Hypothese von „Familienwerten“ diskutiert.
Die Viskositätskurven von insgesamt fünf technischen Kunststoffen (PA66-Compounds mit Glasfasern) von zwei Herstellern wurden in einem Vergleichsdiagramm dargestellt. Zudem wurde ein ungefülltes, schnell erstarrendes PA66 bewertet. In Abbildung 4 werden die schergeschwindigkeitsabhängigen Viskositätsbereiche vergleichend dargestellt.
Die gewählten Compounds mit einem Glasfasergehalt von 50 Gew.-% zeigen herstellerabhängig zwar eine ähnliche Scherabhängigkeit, sie haben in der Höhe der Viskosität jedoch deutliche Unterschiede, bei niedrigen Schergeschwindigkeiten um etwa das fünffache und bei hohen Geschwindigkeiten um das 30-fache. Das Compound des Herstellers B ist insgesamt deutlich niederviskoser. Eine Rezeptur des Herstellers A mit 35 Gew.-% Glasfasern bestätigt zunächst die Annahme einer niedrigeren Viskosität bei weniger Füllgehalt. Dieses Verhalten gilt jedoch nur bei niedrigen Schergeschwindigkeiten bis ca. 500 (s-1), danach fließen die Varianten mit 35 und 50 Gew.-% Fasern sehr ähnlich. Bei einem Glasfasergehalt von 30 Gew.-% des Herstellers B zeigt sich überhaupt nicht, dass ein niedrigerer Fasergehalt auch die Viskosität reduzieren würde. Im Gegenteil - das Compound reagiert durchweg höher viskos und wird, wie die Variante mit 50 % bei hohen Schergeschwindigkeiten, sehr niederviskos. Abschließend wurde ein ungefülltes PA66 des Hersteller B verglichen, das bei der Argumentation zu steigender Viskosität bei steigendem Füllgrad sehr niedrige Werte aufweisen müsste. Dies konnte aus der
Materialbeschreibung jedoch ebenfalls nicht abgeleitet werden. Auch die Abhängigkeit von der Schergeschwindigkeit lässt keine Abhängigkeit erkennen.
Wird dieses Potenzial nicht erkannt, bleibt die Materialcharakterisierung zunächst hauptsächlich ein Kostenfaktor. Dabei stellt sich die Frage, ob sich aus einer Familie ähnlicher Rezepturen rein rechnerisch eine „Familien-Abhängigkeit“ ermittelt lässt, die diesen Kostenfaktor reduzieren würde. Nach dieser Vorstellung charakterisiert ein Hersteller von Compounds eine Rezeptur, mit zum Beispiel 20 % und 50 % Glasfasern, rheologisch und werkstofflich. Die Werte „dazwischen“ werden mehr oder weniger als linear annehmen und entsprechend abgeschätzt. Ähnliche Überlegungen am Markt fordern unter Verwendung der gleichen Argumente, den Einfluss von Masterbatches (hoch konzentrierten Farb- oder Additiv-Compounds) in einem Materialdatensatz zu berücksichtigen. Der Einfluss von Farben und Additiven solle nicht extra gemessen werden, sondern einfach durch Grundeigenschaften und Dosierung abgeschätzt werden.
Diese Forderung zur Reduzierung des Mess-Aufwands soll anhand der Viskositäten und des Erstarrungsverhaltens technischer Kunststoffe (PA66-Glasfasercompounds) mit unterschiedlichen Fasergehalten und verschiedener Hersteller bewertet werden. Hierfür werden vorhandene Messwerte ähnlicher technischer Compounds ausgesucht und in Vergleichsdiagramme überführt. Anhand der Fasergehalte werden die Fließ- und Erstarrungsdaten verglichen und bezüglich der Hypothese von „Familienwerten“ diskutiert.
Die Viskositätskurven von insgesamt fünf technischen Kunststoffen (PA66-Compounds mit Glasfasern) von zwei Herstellern wurden in einem Vergleichsdiagramm dargestellt. Zudem wurde ein ungefülltes, schnell erstarrendes PA66 bewertet. In Abbildung 4 werden die schergeschwindigkeitsabhängigen Viskositätsbereiche vergleichend dargestellt.
Die gewählten Compounds mit einem Glasfasergehalt von 50 Gew.-% zeigen herstellerabhängig zwar eine ähnliche Scherabhängigkeit, sie haben in der Höhe der Viskosität jedoch deutliche Unterschiede, bei niedrigen Schergeschwindigkeiten um etwa das fünffache und bei hohen Geschwindigkeiten um das 30-fache. Das Compound des Herstellers B ist insgesamt deutlich niederviskoser. Eine Rezeptur des Herstellers A mit 35 Gew.-% Glasfasern bestätigt zunächst die Annahme einer niedrigeren Viskosität bei weniger Füllgehalt. Dieses Verhalten gilt jedoch nur bei niedrigen Schergeschwindigkeiten bis ca. 500 (s-1), danach fließen die Varianten mit 35 und 50 Gew.-% Fasern sehr ähnlich. Bei einem Glasfasergehalt von 30 Gew.-% des Herstellers B zeigt sich überhaupt nicht, dass ein niedrigerer Fasergehalt auch die Viskosität reduzieren würde. Im Gegenteil - das Compound reagiert durchweg höher viskos und wird, wie die Variante mit 50 % bei hohen Schergeschwindigkeiten, sehr niederviskos. Abschließend wurde ein ungefülltes PA66 des Hersteller B verglichen, das bei der Argumentation zu steigender Viskosität bei steigendem Füllgrad sehr niedrige Werte aufweisen müsste. Dies konnte aus der
Materialbeschreibung jedoch ebenfalls nicht abgeleitet werden. Auch die Abhängigkeit von der Schergeschwindigkeit lässt keine Abhängigkeit erkennen.
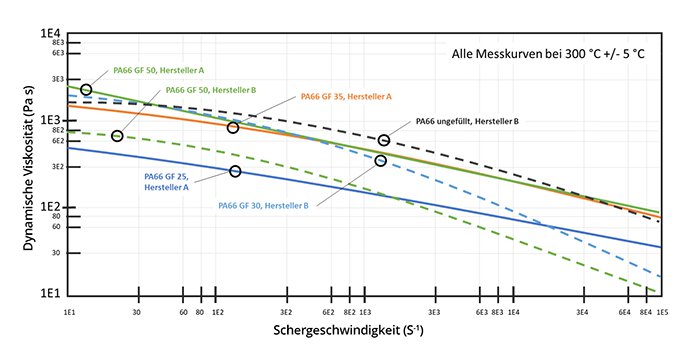
Abbildung 4: Vergleichende Darstellung der scherabhängigen Viskosität unterschiedlicher Glasfasergehalte von PA66 [1]
Die Viskositätsverläufe unterschiedlicher Glasfasergehalte der Compounds gehorchen also keinem der Temperatur ähnlichen Verschiebungsprinzip. Die jeweiligen Hersteller setzen ihre Rezepturen durch Molekulargewichte, Additive und Gleitmittel vermutlich so zusammen, dass diese für die Markennamen jeweils typischen Verarbeitungseigenschaften aufweisen. Auch die Herstellbedingungen bei der Compoundierung haben zahlreiche Einflüsse, abhängig von Rezeptur oder einer anzunehmenden Scherüberhöhung durch den jeweiligen Anteil an Glasfasern.
Die Vermutung der Änderung der Viskosität bei unterschiedlichen Glasfasergehalten nach einem Verschiebungsprinzip kann der durchgeführten Prüfung daher auf Basis der Betrachtung der Werte in den Datenbanken nicht standhalten.
Erfahrungsgemäß ist zu vermuten, dass eine vom Hersteller theoretisch komplett neu aufgelegte Produktreihe eines faserverstärkten Thermoplasts einem solchen Verschiebungsprinzip ebenfalls nicht gehorchen würde. Rezepturen und Produktionseinflüsse ließen sich höchstwahrscheinlich über eine Compoundfamilie hinweg nicht so konstant halten, dass sich die resultierenden Viskositäten rein rechnerisch darstellen ließen.
Aus dem Vergleich der Fließkurven kann auch abgeleitet werden, wie ungenügend eine Bewertung des MFI sein kann. Ein MFI-Vergleich könnte dazu verleiten, anzunehmen, dass sich die Verarbeitung von PA66 GF 30 des Herstellers B (hellblau) nicht sehr von der ungefüllten Variante (dunkelgrau) unterscheidet, da die Nullviskositäten bei geringen Scherraten sehr ähnlich sind. Werden jedoch die Viskositäten bei 1E4 s-1 gegenübergestellt, ergibt sich ein Unterschied um das rund Dreifache. Ein solches Material als Alternative, würde beim Spritzgießen erhebliche Schwierigkeiten verursachen.
Nach dem Fließprozess ist die Erstarrung aus der Schmelze, dargestellt durch die druck- und temperaturabhängige Volumenänderung (Erstarrungsschwindung, pvT), ein wesentlicher Faktor der Prozessauslegung. Es ist prozessbestimmend, bei welchen Temperaturen und Drücken das Compound erstarrt. Am Beispiel der gleichen teilkristallinen, glasfasergefüllten Compounds, soll das Materialverhalten in einem pvT-Vergleichsdiagramm dargestellt und bewertet werden.
Die Vermutung der Änderung der Viskosität bei unterschiedlichen Glasfasergehalten nach einem Verschiebungsprinzip kann der durchgeführten Prüfung daher auf Basis der Betrachtung der Werte in den Datenbanken nicht standhalten.
Erfahrungsgemäß ist zu vermuten, dass eine vom Hersteller theoretisch komplett neu aufgelegte Produktreihe eines faserverstärkten Thermoplasts einem solchen Verschiebungsprinzip ebenfalls nicht gehorchen würde. Rezepturen und Produktionseinflüsse ließen sich höchstwahrscheinlich über eine Compoundfamilie hinweg nicht so konstant halten, dass sich die resultierenden Viskositäten rein rechnerisch darstellen ließen.
Aus dem Vergleich der Fließkurven kann auch abgeleitet werden, wie ungenügend eine Bewertung des MFI sein kann. Ein MFI-Vergleich könnte dazu verleiten, anzunehmen, dass sich die Verarbeitung von PA66 GF 30 des Herstellers B (hellblau) nicht sehr von der ungefüllten Variante (dunkelgrau) unterscheidet, da die Nullviskositäten bei geringen Scherraten sehr ähnlich sind. Werden jedoch die Viskositäten bei 1E4 s-1 gegenübergestellt, ergibt sich ein Unterschied um das rund Dreifache. Ein solches Material als Alternative, würde beim Spritzgießen erhebliche Schwierigkeiten verursachen.
Nach dem Fließprozess ist die Erstarrung aus der Schmelze, dargestellt durch die druck- und temperaturabhängige Volumenänderung (Erstarrungsschwindung, pvT), ein wesentlicher Faktor der Prozessauslegung. Es ist prozessbestimmend, bei welchen Temperaturen und Drücken das Compound erstarrt. Am Beispiel der gleichen teilkristallinen, glasfasergefüllten Compounds, soll das Materialverhalten in einem pvT-Vergleichsdiagramm dargestellt und bewertet werden.

Abbildung 5: Vergleichende Darstellung der druck- und temperaturabhängigen Volumenänderung und Erstarrungspunkte unterschiedlich hoher Glasfasergehalte von PA66 [1]
In Abbildung 5 sind die pvT-Kurven der bereits diskutierten Materialien dargestellt. In den Diagrammen entsprechen diese den grundsätzlichen physikalischen Gesetzmäßigkeiten, dass mit steigendem Glasfasergehalt die Kurven niedriger liegen, also eine höhere spezifische Dichte aufweisen, da die Glasfaser deutlich schwerer ist als das Polymer. Diese Abhängigkeit ließe sich zwar aus einem Fasergehalt vorhersagen, jedoch ist das allein kein hinreichender Aspekt des Materialverhaltens, um die Erstarrung aus der Schmelze vorherzusagen. Der relevante Kennwert ist die Erstarrungstemperatur, also der abknickende Kurvenbereich, bei dem sich die Kristallite erstmals ausbilden. Dieser gehorcht bei den betrachteten Rezepturen erneut keiner Regelmäßigkeit. Es ist davon auszugehen, dass Rezepturbestandteile, wie beispielsweise Nukleierungsmittel, den Charakter der Erstarrung maßgeblich bestimmen und das Erstarrungsverhalten nicht in einer rechnerisch zu ermittelnden Gesetzmäßigkeit liegt. Dies gilt auch für die anderen in Compounds verwendeten Zusatzstoffe und ihre typischen Bestandteile wie Transparenzverstärker (<< 1%), Gleitmittel (< 1%), Entformungsmittel (<< 1%), optische Aufheller (um 1%), Farbmittel (< 10%), Vernetzer (< 10%), Chemische Treibmittel (< 5%), Flammschutzmittel (< 50%), biozide Wirkstoffe (< 10%), Emulgatoren (< 10%), Antistatika (um 1 %) oder Recycling-Additivpakete (< 10%) [2].
Fazit
Familienwerte für technisch ähnliche Compounds auf Basis von wenigen Messungen zu erstellen und weitere Werte daraus zu iterieren, kann aus den in dieser Untersuchung beschriebenen Gründen nicht als aussichtsreich bewertet werden. Aussagekräftige Ergebnisse der rechnergestützten Produktentwicklung basieren zu einem großen Teil auf verlässlichen Materialdaten, welche in ihrer Herkunft und ihrer Stabilität beim Produktionsprozess einschätzbar und durch eigene Validierungsversuche nachgewiesenermaßen tauglich sind. Durch die zu respektierende Vertraulichkeit der Rezepturen von Compounds und Masterbatches erscheint es nicht aussichtsreich, grundsätzliche und übergeordnet gültige Abhängigkeiten zwischen den Inhaltsstoffen einer Zusammenstellung und ihren Fließ- und Erstarrungseigenschaften abzuleiten. Materialkarten aus den Laboren der jeweiligen Anbieter der CAE-Software bieten unserer Meinung nach die beste Möglichkeit zur gelungenen digitalen Produktentwicklung.
Das SimpaTec Expertenteam steht Ihnen bei der Auswahl von Materialien, deren Charakterisierung und der Übertragung in die MOLDEX3D®-Datenbank zur Verfügung. Überzeugen Sie sich selbst wie die SimpaTec, durch Kombination qualitativ hochwertiger Simulation und kundennaher Beratungsdienstleistung, ein kompetenter Partner für die kunststoffverarbeitende Industrie sein kann und den Weg zur Produkt- und Prozessoptimierung möglichst kurz und effizient gestaltet.
Das SimpaTec Expertenteam steht Ihnen bei der Auswahl von Materialien, deren Charakterisierung und der Übertragung in die MOLDEX3D®-Datenbank zur Verfügung. Überzeugen Sie sich selbst wie die SimpaTec, durch Kombination qualitativ hochwertiger Simulation und kundennaher Beratungsdienstleistung, ein kompetenter Partner für die kunststoffverarbeitende Industrie sein kann und den Weg zur Produkt- und Prozessoptimierung möglichst kurz und effizient gestaltet.
Autor:
Dr.-Ing. Michael Bosse, Technical Sales, SimpaTec Engineering GmbH, Aachen
Literatur:
[1] Materialdatenbank CoreTech System Co. Ltd. “Moldex3D”, Release 2023R3OR
[2] Michael Bosse, Vorlesung “Aufbereitung von Compounds”, Technische Hochschule Würzburg-Schweinfurt, 2022
[3] Zulkifli Mohamad Ariff, Azlan Ariffin, Suzi Salwah Jikan and Nor Azura Abdul Rahim (2012). Rheological Behaviour of Polypropylene Through Extrusion and Capillary Rheometry, Polypropylene, Dr. Fatih Dogan (Ed.), ISBN: 978-953-51-0636-4, InTech, Verfügbar unter: https://www.intechopen.com/books/polypropylene/rheological-behaviour-of-polypropylene-through-extrusionand-capillary-rheometry
Copyright:
_ Moldex3D ist ein eingetragenes Warenzeichen der Firma CoreTech System Co., Ltd., Taiwan.
_ Foto (Header) mit freundlicher Genehmigung Carl Hanser Verlag GmbH
Dr.-Ing. Michael Bosse, Technical Sales, SimpaTec Engineering GmbH, Aachen
Literatur:
[1] Materialdatenbank CoreTech System Co. Ltd. “Moldex3D”, Release 2023R3OR
[2] Michael Bosse, Vorlesung “Aufbereitung von Compounds”, Technische Hochschule Würzburg-Schweinfurt, 2022
[3] Zulkifli Mohamad Ariff, Azlan Ariffin, Suzi Salwah Jikan and Nor Azura Abdul Rahim (2012). Rheological Behaviour of Polypropylene Through Extrusion and Capillary Rheometry, Polypropylene, Dr. Fatih Dogan (Ed.), ISBN: 978-953-51-0636-4, InTech, Verfügbar unter: https://www.intechopen.com/books/polypropylene/rheological-behaviour-of-polypropylene-through-extrusionand-capillary-rheometry
Copyright:
_ Moldex3D ist ein eingetragenes Warenzeichen der Firma CoreTech System Co., Ltd., Taiwan.
_ Foto (Header) mit freundlicher Genehmigung Carl Hanser Verlag GmbH