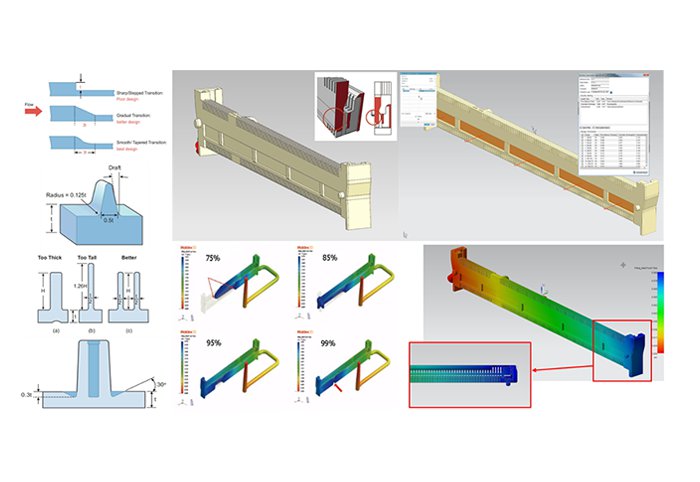
Ermittlung des optimalen geometrischen Produktdesigns in kürzester Zeit
SPEZIELL FÜR UNSERE ANWENDEREin allgemeiner Herstellungsprozess für Kunststoffprodukte umfasst viele Stufen, darunter Produkt- und Strukturdesigns, Werkzeugdesigns, Werkzeugbau, Produktion und Qualitätsprüfung. Ist das Bauteildesign nicht Spritzguss gerecht ausgelegt, führt dies zu Schwierigkeiten in der Produktion oder zu einem erhöhten Kommunikationsaufwand für Designänderungen sowie die Anpassung des Bauteils und Werkzeugs. Eine Analyse mit Moldex3D bereits während der Entwurfsphase des Kunststoffprodukts, um sich den optimalen Entwürfen anzunähern, mindert diese potenziellen Probleme und gewährleistet eine reibungslosere Massenproduktion.
In der Regel werden in der Produktentwicklungsphase Prüfungen im Rahmen des „Design for Manufacturing“ (DFM) durchgeführt. Übliche DFM-Punkte, die überprüft werden, sind z. B. die Schwindungswerte von Kunststoffen, Entformungswinkel und die Frage ob Hinterschnitte auftreten. Ein weiterer wichtiger Punkt sind Dickenverteilung, sowie Rippen- und Nabenform. Diese Prüfungen können anhand von CAD-Funktionen oder manuellen Prüfzeichnungen durchgeführt werden. Obwohl normalerweise auf eine gleichmäßige Wandstärkenverteilung geachtet wird, werden bei erforderlichen Dickenabweichungen Konstruktionen vorgeschlagen, wie in der Abbildung (links) schematisch dargestellt. Auf der anderen Seite zeigt die Abbildung auch die vorgeschlagenen Designs von Rippen und Vorsprüngen. Das Kunststoffspritzgießen ist jedoch ein dynamischer Prozess, ein und derselbe Kunststoff von verschiedenen Herstellern und mit verschiedenen Zusatzstoffen, kann große Unterschiede in den Materialeigenschaften aufweisen. Darüber hinaus haben verschiedene Spritzgießmaschinen ein unterschiedliches Ansprechverhalten, sowie unterschiedliche technische Bedingungen, welche die Produktqualität beeinflussen kann. Infolgedessen treten in der tatsächlichen Fertigung selbst mit DFM immer noch Probleme auf. Obwohl der Entwickler beispielsweise die Vorschläge für die Bauteilstärken und die Rippenkonstruktion befolgt hat, können die Endprodukte immer noch übermäßigen Verzug und geringe strukturelle Festigkeit aufweisen. Oberflächenfehler oder sogar eine unvollständige Füllung können die Folge sein und die Produktion wird nicht in der Lage sein das Produkt herzustellen.
Somit stehen keine allgemein gültigen Regeln für alle Produktentwürfe zur Verfügung. Neben der Verwendung von CAD-Software zur Durchführung von DFM-Prüfungen können Analysen von CAE-Simulationen bei der Anpassung der geometrischen Abmessungen, der Validierung der optimierten Konstruktionen und der iterativen Fehlerbehebung helfen. Solche iterativen Designänderungen und -validierungen sind ein langwieriger Prozess. Um diese Herausforderung zu meistern unterstützt die Moldex3D-Werkzeugkette (z.B. SYNC, DOE ...) von 2021 die Geometrieoptimierungswerkzeuge und hilft den Benutzern, den CAE-Analyse-Workflow erheblich zu vereinfachen. Mit dieser Werkzeugkette können die Entwürfe mit allen Abmessungsvarianten und die entsprechenden CAE-Analyseergebnisse in mehreren einfachen Schritten erstellt werden.
Der in der Abbildung (rechts) gezeigte Fall eines Steckverbinders demonstriert, wie Moldex3D SYNC verwendet werden kann, um geometrisch optimierte Entwürfe zu erhalten. Die Abbildung zeigt das ursprüngliche Produktmodell welches die DFM-Prüfung bestanden hat, und dessen erstes Simulationsergebnis. Wie in der Analyse zu sehen ist, tritt auf beiden Seiten des Verbinders ein Ungleichgewicht auf. Dies zeigt auch das Ergebnis der Verzugsanalyse, welches ein Problem für die Stiftleiste beim Einstecken verursachen würde, was vor der Fertigung verbessert werden muss. Aus dem Querschnitt des ursprünglichen Entwurfs geht hervor, dass beide Seiten unterschiedlich dick sind und das dickere Ende leicht verändert werden muss. Es zeigt sich zwar, dass eine Änderung der Dicke die Fließunwucht und den Verzug verbessern kann (eine Strukturanalyse ist ebenfalls erforderlich), aber der Konstrukteur kann nicht bestimmen, wie viel Änderung erforderlich ist, um die optimale Dicke zu erreichen. Es wäre sehr zeitaufwändig, jedes Design mit unterschiedlicher Dicke zu analysieren. Mit dem Geometrieoptimierungstool in Moldex3D SYNC kann der Benutzer schnell die zu variierenden Parameter angeben und alle Analysegruppen einstellen und so eine Reihe von optimalen Analyseergebnissen erzielen, bei denen der Verzug verbessert wurde, während die Schmelzfront am Ende zusammenläuft.
Sie möchten mehr erfahren? Bitte wenden Sie sich an: 0241 565 276-0 oder senden Sie eine Email an info@simpatec.com .