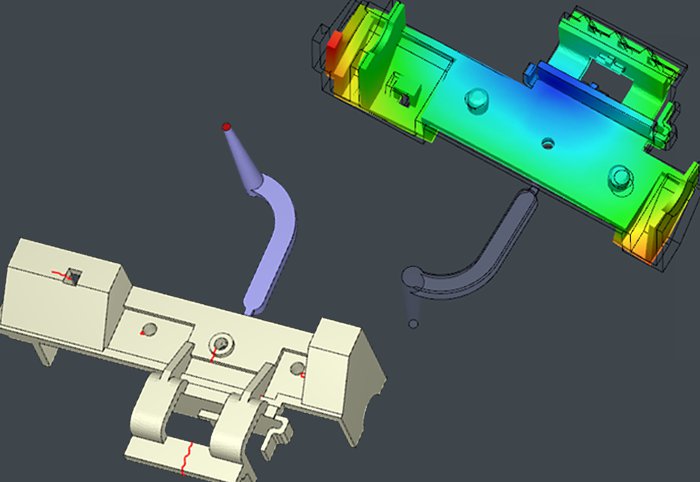
Fehler beim Spritzgießen und die dadurch entstandenen strukturellen Bauteilschwächen (Teil 2)
SPEZIELL FÜR UNSERE ANWENDERHaben Sie unerwartete Ausfälle bei der Montage Ihres Bauteils? Dies kann auf Probleme in der Produktion zurückzuführen sein z.B. Bindenähte und Lufteinschlüsse. Heute erfahren Sie, wie Sie diese Fehler mit Hilfe von Moldex3D identifizieren und eliminieren. Im ersten Artikel wurden Lufteinschlüsse, Verbrennungen und Einfallstellen erklärt. Heute stehen Bindenähte und Verzug im Fokus und wie diese vermieden werden können …
Während des Füllvorgangs, wenn die Schmelze in zwei oder mehr Fronten zusammenläuft und abkühlt, können Bindenähte im Bauteil entstehen (Bild links). Die Ursache für Bindenähte liegt in der Aufspaltung und Wiedervereinigung der Schmelze, z. B. durch mehrere Anschnitte, unterschiedliche Wandstärken oder umfließen von Hindernissen. Die Folge ist eine optische und/oder mechanische Schwächung des Bauteils.
Je nach Ursache können eine oder mehrere Lösungen zur Vermeidung von Bindenähten eingesetzt werden. Diese können in drei Kategorien eingeteilt werden:
Prozessbedingung:
__ Werkzeugtemperatur und Schmelzetemperatur erhöhen.
__ Einspritzgeschwindigkeit erhöhen (Füllzeit reduzieren).
Material:
__ Verwendung von faserverstärkten oder niederviskosen Materialien.
Bauteil- und Werkzeugdesign:
__ Überarbeiten Sie das Angussdesign.
__ Überarbeiten Sie die Wandstärke des Teils.
Eine Erhöhung der Werkzeugtemperatur und der Schmelzetemperatur kann die Bauteilfestigkeit an Bindenähten erhöhen, wenn diese nicht vermieden werden können. Man kann die Temperatur an einer Bindenaht überprüfen, indem Messknoten platziert werden. Die Temperaturverteilung kann anschließend mit dem Messknoten-Assistenten in Moldex3D betrachtet werden. Obwohl eine Erhöhung der Temperatur an den Bindenähten deren Erscheinungsbild vermindern kann, wird empfohlen diese Strategie als letzten Ausweg in Betracht zu ziehen, da eine erhöhte Schmelzetemperatur den Verzug negativ beeinflussen kann.
Der Verzug ist die nächste zu berücksichtigende Herausforderung (Bild rechts), die bei der Montage zu strukturmechanischer Belastung führen kann. Dieser tritt auf, wenn verschiedene Zonen eines Bauteils unterschiedlich schwinden. Dabei entstehen unterschiedliche Spannungen, die zu einem Verbiegen bzw. Verdrehen des fertigen Bauteils beim Abkühlen führt. Wenn das Bauteil unterschiedlich gekühlt wird, kann dies ebenfalls zu Verzug führen. Um die, durch die Form verursachte Abkühlungsdifferenz, im Bauteil zu überprüfen, gibt es in Moldex3D das Ergebnis "Mold Temperature Difference". Der erhaltene Wert sollte kleiner als 5% sein damit eine gleichmäßige Abkühlung gewährleistet wird.
Außerdem ist bei teilkristallinen Materialien, wenn die Moleküle versuchen sich zu relaxieren, eine ungleichmäßige Schwindung zu erwarten. Daher kann nicht nur die richtige Werkzeugtemperatur und Abkühlzeit, sondern auch das richtige Material eine Lösung zur Optimierung des Verzugs sein.
Sprechen Sie uns an 0241 565 276 0 oder Senden Sie eine Email an info@simpatec.com.