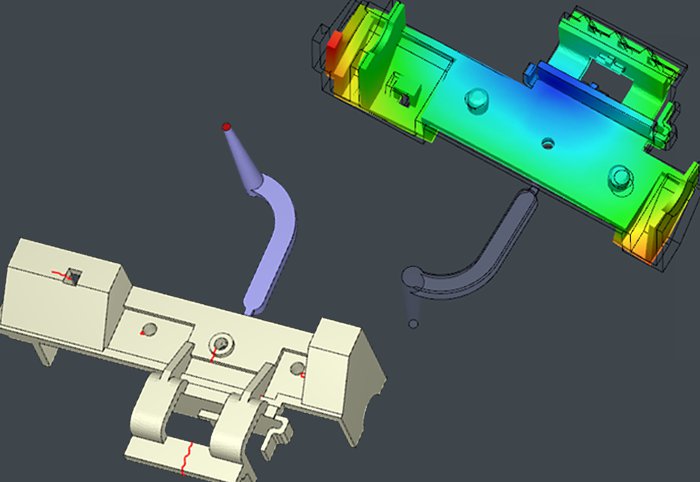
Molding failures and structural weaknesses (part 2)
ESPECIALLY FOR OUR USERSDo you notice unexpected failure during assembly of your part? This could be due to unexpected problems during production (e.g. weld lines, air traps, …). In this serie, you can see how these failures can be detected and handled in Moldex3D. In the first part, air traps, burn marks, and sink marks were explained. Today, we will talk about weld lines, warpage and how to avoid them.
During the filling, when the melt converges in two or more fronts and cools down a weld line can appear in the part (image left). The cause of weld lines lies in splitting and reunification of the melt e.g. due to multiple gates, different wall thicknesses or flowing around obstacles. The result is optical and mechanical weakness in the part.
Depending on the cause, one or more solutions can be used to prevent weld lines. The solutions can be categorized into three:
Process condition:
__ Increase mold temperature and melt temperature.
__ Increase injection speed (reduce filling time).
Material:
__ Using fiber-reinforced or low-viscosity materials.
Part and mold design:
__ Revise the runner design.
__ Revise the thickness of the part.
Increasing the mold temperature and melt temperature can increase the part strength at weld lines, when they can not be avoided. In order to screen the temperature at a weld line, measure nodes can be placed to observe the temperature distribution using Measure Node Wizard in Moldex3D. Although increasing the temperature at the weld lines may diminish their appearance, it is recommended to hold this strategy as the last resort since increased melt temperature will likely aggravate the warpage.
Another common molding failure is warpage (image right) which occurs when different parts of a component shrink differently. This uneven stress results in bending or twisting of the finished part as it cools. If the part is cooled differently this can also yield to warpage. To check the cooling difference caused by mold in the part there is an option in Moldex3D called “Mold Temperature Difference” in cooling results. The obtained value should be less than 5% for an even cooling.
In addition, in highly oriented materials such as semi-crystalline materials, when molecules try to relax, an uneven shrinkage can be expected. Therefore, not only proper mold temperature, cooling time, but also proper material can be a solution for warpage.
For further information please contact us at 0241 565 276 0 or send an email to info@simpatec.com.