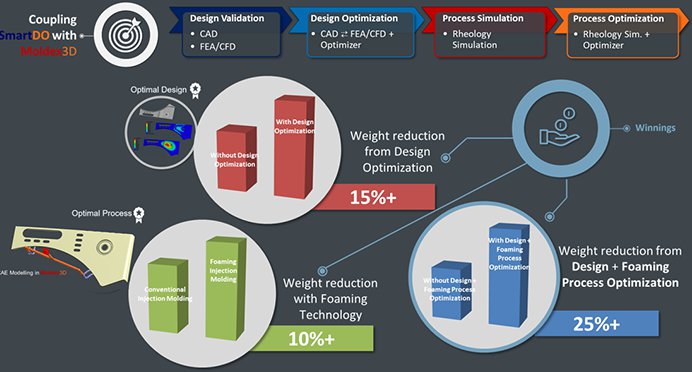
Components optimized, cost-efficient and dimensionally stable - with SmartDO!
ESPECIALLY FOR OUR USERS
Still struggling on realizing a brilliant design with injection molding? Difficult to optimize the process for dimensional stability of your plastic part? Would like to implement Foam Injection Molding technique but afraid of the complex setting? We have a tool to ease your headache. It can find its own way to the target. Interested? Let’s have a look!
In the previous article, we revealed that using SmartDO in Design Optimization, 16% weight reduction could be easily achieved for a washing machine cover without sacrificing its mechanical behavior. That’s only the first step. In the following manufacturing stage, we will show you what can be done further for Process Optimization.
To produce a plastic cover, injection molding is the ideal approach, fast and productive. Nevertheless, there are several parameters that impact the ability of manufacturing and the quality of the part. For example, injection speed controls filling time of the part and also results in different injection pressure. „Can my injection machine withstand the fast injection speed without reaching the pressure limit? “ is one of the common questions. On top of that, while adding process window into consideration, such as melt temperature, mold temperature, etc., the challenge becomes more difficult. And this is not the only challenge for injection molding.
The combination of plastic and injection molding would intrinsically deflect a part owing to plastic properties, design and molding layout and process control. However, a plastic cover is designed to be assembled somewhere else with a tight tolerance for deflection. A well-designed cooling system plus good process control could lower the deflection to a certain level, a common practice in traditional injection molding. But to go further, we need to have a technique beyond traditional one. And Foam Injection Molding is the answer.
Different to the traditional injection which maintains the part dimension by compacting plastics externally, Foam Injection Molding is compacting the part internally by gas bubbles. Part deflection can be reduced dramatically but the complexity of process control increases significantly as well. All of the process parameters should be conformed with the gas dosing amount. We have to reach a well-balanced parameter set to get an excellent outcome. That’s the challenge. But we could sort it out and optimize it by using SmartDO.
Here are what we set – Filling time, melt temperature, Mold temperature, VP switch, Gas dosage amount, Foaming duration and Cooling time are the key parameters that impact the part quality and the machine capability. We need to find an optimal set of them.
Each machine has ist limitation, therefore we limit the maximum injection pressure to 100MPa, and maximum clamping force to 180Ton. To have the cover assembled without problem, shrinkage between two ends on the longest edge should not exceed 0.65%.
And don’t forget, our mission is still „Lightweight “. „An optimal set of parameters for the lightest part with the limitations for manufacturing and assembly “is our ultimate goal.
What are the results? we found the optimal parameter set with 10.6% weight reduction with maximum injection pressure 78.3Mpa, maximum clamping force 123.4Ton and shrinkage 0.55% (all within the limitations!).
In conclusion, throughout the whole process, SmartDO finds us 16% weight reduction in Design Optimization stage, then 10.6% weight reduction in Process Optimization, more than 25% weight reduction in total! Amazing, isn’t it?
Interested in learning more about SmartDO? Please contact us: 0241 565 276-0 or send an email to info@simpatec.com .