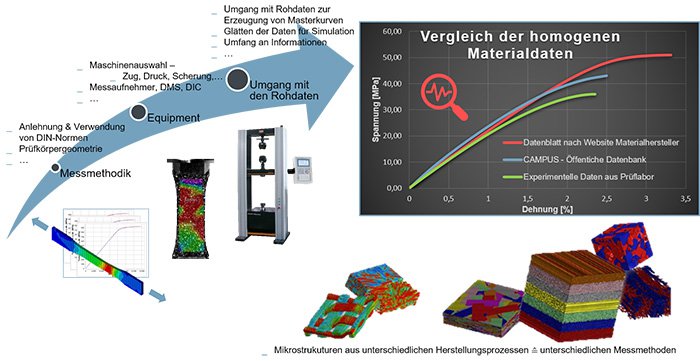
Requirements regarding the mechanical material card for optimal quality results for FE analyses
ESPECIALLY FOR OUR USERS
Discrepencies between simulation and experimental tests can be caused by different reasons. The most common reason concerns the quality of the material parameters for the creation of the material card. Use our know-how to achieve your goal.
Simulations are well-established in the development of component design, manufacturing process and structural mechanical design. By means of numerical calculations, profound knowledge about the component behavior as well as the manufacturing process can be gained for further optimization. In order to consistently validate and verify the simulations afterwards, experimental tests are generally carried out on prototypes. Often critical areas or unexpected component behavior are detected in practice and cause high costs due to unnecessary change loops in tool design or component design.
The causes for any unexpected behavior in the manufacturing process or component behavior can often be found in the material cards used for the simulation tools. The input data for the creation of material cards determine the quality and significance of a simulation. In addition, coordinated material characteristics are required for the different questions of an FE analysis. In the field of composites fiber orientation as well as the microstructure plays a decisive role. The material behaviour knows at different conditions like e.g: temperature or strain rate dependence. For this reason, the characterization of the material properties and the scope of the tests related to the application are the basis for successful predictions and calculations - tensile, compression or shear testing.
The same importance must be given to the measuring method, the material characteristics to be characterized. A classical tensile test is no longer sufficient in many fields of application, since viscoelasticity is necessary to considerf e.g. creep. On the other hand, for high strain rates, a DIC system is usually required to record local strains during testing for higher accuracy. Thus, the complexity of the application and the significance of the results define the requirements for an optimal material map.
To avoid unnecessary characterizations and costs, an exchange of specialists in interdisciplinary teams takes place. This means that structural mechanics are in contact with material specialists as well as process engineering and together they define the required input and the measurement methodology for simulations.
Finally, individual material cards for applications are created with which qualified statements can be made and the possible optimization potential can be revealed.
Not every company has the required know-how directly at hand. We are happy to support you in terms of consulting and with the implementation from characterization up to calibrated material cards for direct use in our in-house simulation tools.