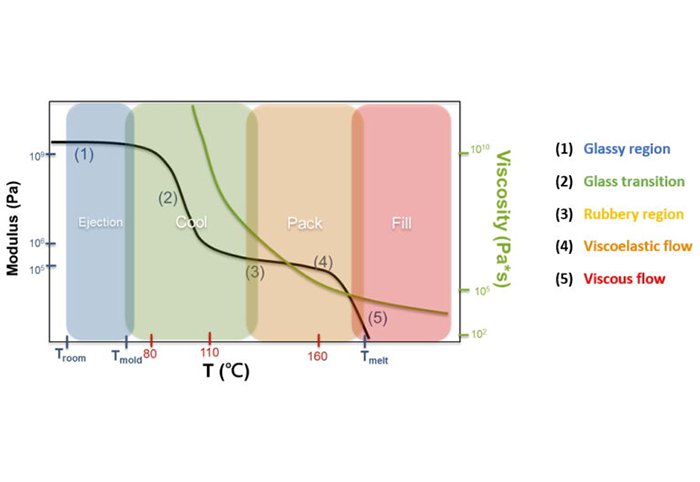
Successful Viscoelastic Flow Simulation Requires Reliable Rheological Data
EXPERT-TIP
Rheological behavior is one of the most complex and important properties in polymer processing. To complete a successful process simulation, reliable material data and models are necessary. The polymer flow can be predicted reasonably well with the assumption of inelastic (generalized Newtonian) fluids and the data from the capillary rheometer. However, the inelastic analysis may fail to describe the viscoelastic phenomena because polymers are viscoelastic in nature …
The typical curve of modulus and viscosity of an amorphous polymer is shown in the above picture Basically, the elastic behavior gets more and more significant relative to the viscous behavior with the decrease of temperature. According to polymer physics, the state of a polymer can be divided into five regions. (1) glassy region; (2) glass transition; (3) rubbery region; (4) viscoelastic flow; (5) viscous flow. In the viscous region (5) the inelastic (or generalized Newtonian) model is the proper model to simulate the fluid flow. The elastic start to become more and more important from the viscoelastic flow region to the rubbery region. The material behaves more and more solid-like (elastic) from glassy transition to the glassy region.
In the filling stage, melt temperature is usually higher than the nozzle temperature because of viscous heating, the temperature falls in the viscous flow region indicating the inelastic (generalized Newtonian) models can be employed. In the packing stage, the melt temperature starts to cool down and it changes from viscoelastic to rubbery, which indicates the elastic behavior starts to play a crucial role. After packing, polymer goes through glass transition in the cooling stage and reaches the glassy region in the ejection stage.
In addition to a stable viscoelastic solver, reliable material data and parameters of the mathematical model are necessary to complete a successful viscoelastic flow simulation.
Generally, the filling in injection molding is considered to have a high shear rate and high-temperature flow. Therefore, the capillary rheometer is generally the ideal instrument to characterize the flow behavior. However, there are certain regions in the cavity, such as the core layer or thick area, where the flow is under a low shear rate. In addition, the low temperature would be observed in the skin layers especially in the packing stage.
Consequently, the viscosity data only from the capillary rheometer may not be enough to describe the whole process precisely. To extend the range of shear rate and temperature, parallel-plate and capillary rheometer are both employed. In addition, polymer melts with similar shear behavior may show very different extensional behavior especially for highly branched polymer.
Interested?! Please contact us at 0241 565 276-0 or send an email to info@simpatec.com.