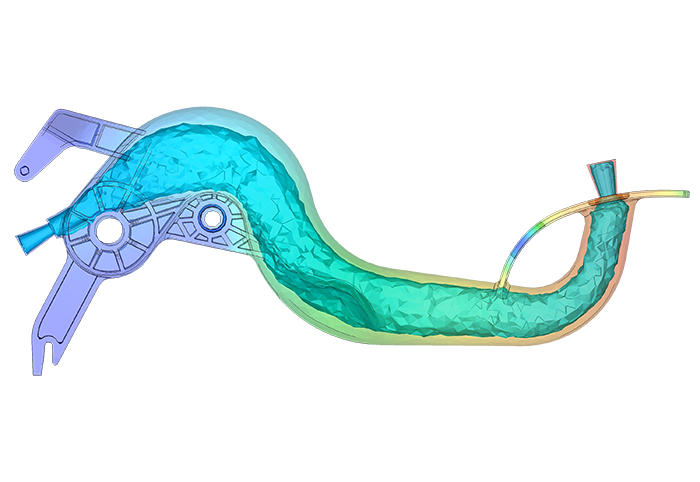
Trailblazing new features and functions – Moldex3D R17
With competence, experience, ambition and the use of the latest software technologies, SimpaTec mutually sets new standards in the holistic development and optimization of processes, components and tools. The capabilities of simulation for injection molding in Moldex3D R17 have been further extended and now offer completely new possibilities for engineers, designers and manufacturers.
The range of recent implementations and novelties includes more comprehensive and realistic simulations to help close the gap between the physical and virtual worlds and an entirely new user interface and unified simulation workflow allow users to gain deeper insights into product performance a lot faster. Not to forget the valuable enhancements made for lightweight components in the automotive and aerospace sectors, as well as the significant improvements in terms of composites simulation solutions. The latest version of Moldex3D R17 definitely accelerates the decision-making process whilst maintaining reliable and accurate results and thus helping part designers and mold makers to efficiently and effectively master their daily work and at the same time still achieving the best possible economic success.
Fluid-assisted injection molding now with push back simulation
Moldex3D GAIM and WAIM modules have undergone substantial refinements and now support simulating push back by illustrating how the melt is pushed by the gas/water back into the molding machine barrel. The functionalities of the latest version R17 allow users to better investigate the gas/water penetration behaviors in order to produce hollow, lightweight parts, reducing material waste and to provide more valuable surface quality than with the short-shot method.
Mold temperature controller advisor
Another enhancement available in Moldex3D R17 can be found within the cooling analysis function. Here users now have the opportunity to precisely evaluate the performance of mold temperature controllers by providing crucial data, including maximum pressure drop, total flow rate and heat dissipation. Through seamless integration between the physical and the virtual worlds, engineers can fully leverage simulation data to make more informed decisions.
Consider Expansion Ratio in PU Chemical Foaming Analysis
A great deal of effort and energy has also been but into developments for the lightweight sector. Technical hurdles have been successfully conquered and for advanced lightweight manufacturing processes, the Moldex3D Material Lab now provides extensive material testing services to characterize critical material parameters, including the expansion ratio of polyurethane foam. Moldex3D R17 offers new opportunities to further predict the expansion ratio in PU chemical foaming analysis to more accurately predict the foam height and shape in order to be able to create polyurethane molded parts of higher quality. Also available in R17 is an improved RTM wizard, which streamlines the mesh preparation process, increasing simulation productivity.
Besides the extensive Moldex3D training program the Germanspeaking SimpaTec Usermeeting taking place on March 24 and 25, 2020 in Bamberg, is also an ideal opportunity to get the latest updates and to convince oneself how SimpaTec can be a competent partner for the plastics processing industry enabling your way to product and process optimization as short and efficiently as possible by combining high-quality simulation and customer-oriented consulting services.