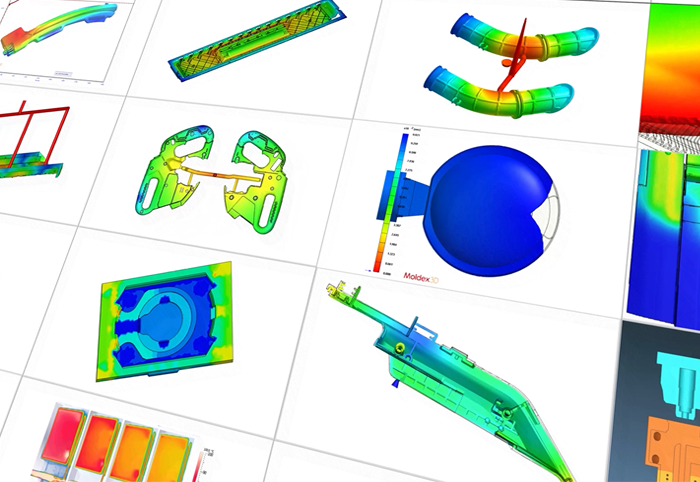
Moldex3D 2024 – Precise, detailed, powerful
FAKUMA - Hall A5, Booth A5-5003
SimpaTec, known as one of the leading engineering and software partners for the plastics processing industry, will be exhibiting again at this year’s FAKUMA in Friedrichshafen. At their booth in hall A5, A5-5003, visitors can expect up-to-date information and the latest technology highlights relating to the holistic development and optimization of plastic components using state-of-the-art software solutions. Moldex3D 2024, the premier software solution for the design and optimization for injection molding processes, as well as all CAx products within SimpaTec’s portfolio – such as Digimat, T-SIM, B-SIM, 3D_Evolution, 3D_Anylyzer and 4D_Additive - provide designers and toolmakers with means to facilitate the design and production of high-quality products while reducing costs and time-to-market.
The plastics industry is facing a new era of competition! With the pursuit of a low-carbon and circular economy as future development goals, a whole new set of opportunities is opening up for the industry. Compared to traditional metal materials plastics are clearly the better choice for the latest industry requirements, including lightweight, energy saving, environmental protection, low manufacturing costs, design flexibility and performance standards. The current release Moldex3D 2024 is THE answer to adhere to these conditions. The software offers advanced simulation solutions to easily map and handle the most complex processes. Furthermore, unique Moldiverse-Cloud-Platform services support users to optimize production processes already in the design phase. This makes Moldex3D 2024 an essential tool in terms of innovation and efficiency.
Precision Electronic Potting Process Simulation
To ensure road safety electric cars are equipped with various sensors that provide drivers with precise vehicle information and safety guarantees. Electronic systems in motor vehicles must be able to withstand harsh environmental conditions such as water, humidity, temperature fluctuations, foreign objects and dust at all times. In order to meet strict product standards simulation can be used to detect and correct production errors more quickly and speed-up commercial launch.
The latest version Moldex3D 2024 introduces the first industry solution to be able to simulate potting of electronic assemblies ('electronic potting'). A variety of process sequences can be mapped using practical modeling tools and specific setting options. Furthermore, it provides the user with a more realistic and detailed visualization of the supply and distribution of the potting material. The physical effects and phenomena are represented by numerical models that account for surface tension and capillary action, thus enabling the simulation of sophisticated and precise potting of electronic component groups, which is referred to as "electronic potting."
Comprehensive Support for Plastic Molding Cloud Services
The latest version of the software increases the scope of services relating to plastic injection molding. The Moldex3D iSLM data management platform has expanded its range of functions and introduces the ‘personal mode’ for individual use and ‘server Mode’ for cross-team collaboration. This means users now have even more flexible modes of use at their disposal. The new release impresses with optimized functions to organize project-related data, improved model comparison functions, greater support for CAD formats, and directly implemented functionalities to calculate the CO2 footprint. The software actively helps users to adhere to the latest CO2 emission standards.
Moldex3D 2024 marks significant enhancements in both the precision of predictions as well as the ability to provide tailor-made solutions. The new release gives an even more detailed and analytical insight into the component, improves the efficiency of weld line and air entrapment calculations as well as the prediction of shrinkage behavior. Bilinear isotropic curing models are also used for reactive injection molding and foaming applications- no doubt Moldex3D is setting new standards.
SimpaTec, operating since 2004, offers custom-made innovative methods and solution concepts in the development and optimization of injection molding components in every stage of the process. This year’s FAKUMA 2024 (hall A5/booth A5-5003) is an ideal opportunity to get the latest updates and to convince oneself of how SimpaTec can be your first contact and your leading consultant to cluster efficient and highly productive software and service packages for the plastics processing industry.