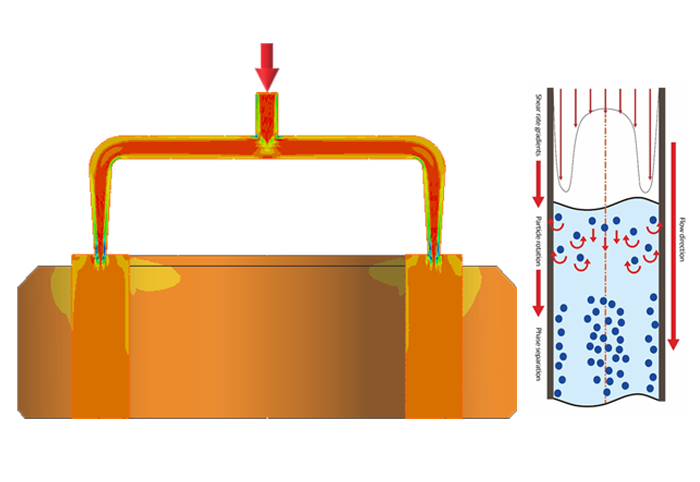
Powder Injection Molding with Moldex3D
ESPECIALLY FOR OUR USERSPowder injection molding presents various indutrial challenge such as surface finish, surface quality and the effects of volume shrinkage, as well as warpage and non-uniform powder concentration. The PIM module in Moldex-3D will be a meaningful support for you in these points to achieve the high standards of product quality.
The PIM process is a variation of metal injection molding in which ceramic powder is also used. It combines all the advantages of plastic injection molding with the advantages of powder metallurgy, such as the near final contour machining of metals and ceramics. The PIM process is often used to ensure the production of components with very complex geometries at very low cost.
The PIM module in Moldex-3D stands for Powder Injection Molding and accompanies you throughout the entire process, i.e. from the filling analysis to the cooling phase and thus helps you to perform shrinkage analyses, for example. Ceramic as well as metallic powders can be used and taken into account. The powder particles are tracked during the simulation via the particle-tracer result, helping you to predict the powder particle concentration, a very critical factor when it comes to determining the position of the black lines, as well as identifying sink marks.
Due to the high shear rate, particles segregate along the cavity wall, known as "low powder concentration". In addition, particles concentrate in the area of minimum shear rate, often in the central area of the flow field.
The simulation of powder injection molding with the PIM module in Moldex3D offers you the full range of results for the simulation of metal and ceramic injection molding. This allows you to efficiently and specifically analyze the effects of volume shrinkage, warpage and black lines and take targeted countermeasures.
Contact us at 0241 565 276 0 or send an email to info@simpatec.com.