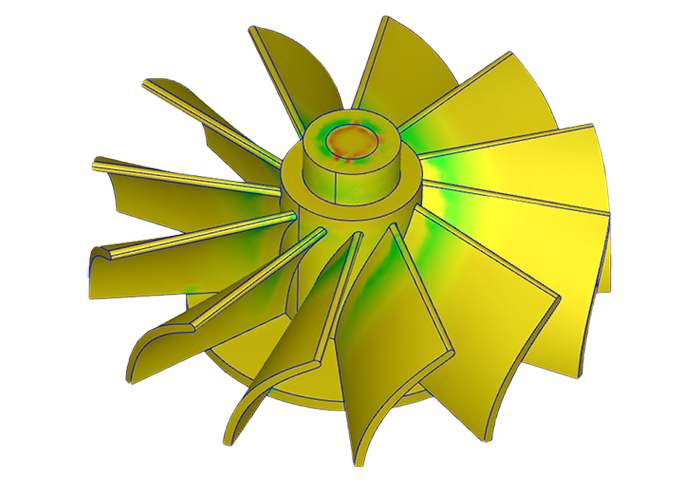
Specaial process - Powder Injection Molding
ESPECIALLY FOR OUR USERS
Do you want to produce medium-sized components with complex geometries made from metal or ceramics, a reliable process is powder injection molding. With Moldex3D's special module PIM (Powder Injection Molding) it is possible to simulate the manufacturing process with metallic or ceramic powders.
In the first process step, fine metal or ceramic powder is mixed with a binder, the so called thermoplastic matrix in order to form a homogeneous mass that can be processed in an injection molding process similar to plastics processing. This metal/plastic mixture is called feedstock. It is injected in liquefied form into a closed mold, where it first completely fills the cavity by means of targeted temperature control and then plasticizes it. The resulting molded body (green compact) already has all the typical geometric features of the finished component. After removing the green body from the injection moulding machine, the binder is removed again in a two-stage process, the debinding process. The result is a purely metallic or ceramic component. The porous molded body, also known as brown compact, which remains after debinding, is compacted by sintering at high temperature to form a component with its final geometric and mechanical properties. The production of the green body can be simulated with Moldex3D.
The structure of the simulation model and the definition of the process parameters are analogous to conventional injection molding. Tooling and temperature control are not absolutely necessary for the simulation, but they ensure a higher accuracy. Differences to conventional injection molding are mainly found in the material data. In order to calculate the powder concentration, a material data set is required that contains information about the type of powder, the density and the average particle size. The powder influences material properties such as viscosity and thermal conductivity.
To achieve an optimal component quality, the powder distribution should ideally be as uniform as possible in the green compact. The distribution of the powder concentration from the filling simulation allows conclusions to be drawn about possible black lines on the component surface.
In case of any further questions, we are at your disposal as usual.