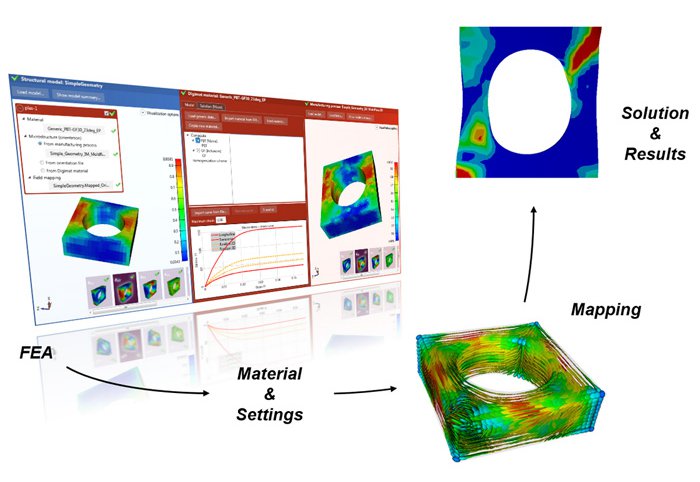
Simulation of structural failure of injection molding parts
ESPECIALLY FOR OUR USERS
Many injection molded products are subjected to mechanical loads during their component life as part of their function. Therefore, an important step is to design the design process of these components in such a way that the expected load does not lead to mechanical failure of the component. For injection molded components (especially fiber-reinforced plastics), the mechanical performance is highly dependent on the manufacturing process. It therefore makes sense to not consider the process and mechanical design separately in the simulation-based design, but to link these simulation steps with each other.
There are various failure scenarios for plastic components, the most important of which include plastic (i.e. irreversible) deformation and the formation of cracks and fractures. These lead to full or partial loss of functionality of the component and must therefore be avoided if possible. These forms of failure do not occur completely independently of each other, e.g. cracks and plastic deformation often lead to fractures, cracks can lead locally to plastic deformation due to stress concentrations at the crack tip.
The factors which lead to mechanical failure can be roughly grouped into four categories which interact with each other in a complex way:
__ External influences: applied mechanical loads (and also the loading rates) and temperature (and also the warming/cooling rates and temperature gradients).
__ Material properties: stiffness and strength, which are in turn dependent on – anisotropies (especially for fiber reinforced plastics), crystallinity, temperature and internal prestresses. It is also important to consider that the martial properties can change (at least locally) during the life cycle of a part due to environmental influences (like contact to fluids and gases or radiation) and other aging processes.
__ The geometry of the part and especially “notchlike” design solutions like inner corners and edges and grooves. These often lead to stress concentrations, which in turn are initiators of tears or plastic deformation.
__ Damages, either introduced during the manufacturing process (for example surface imperfections, weld lines or inclusions) or introduced during the lifecycle of the part (for example scratches).
Software packages for injection molding simulations (like Moldex3D) often have modules which allow to perform a structural analysis based on the finite element method. Those can be used for a first assessment of the mechanical behavior. However, to assess the complex processes which lead to structural failure dedicated structural solvers are necessary. The main reasons for this, among others, are:
__ The nonlinear nature of the problem, which requires the use of specialized non-linear structural solves (like MSC Marc).
__ Injection molding parts are often part of an assembly and modeling of addition components is required to insure a proper load introduction and mechanical behavior of these parts
__ The fact that a mesh, which works fine for an injection molding simulation, is not necessary a good solution for the structural simulation
But the injection molding simulation still play a role in the structural analysis. Like mentioned above, the manufacturing process itself is an important factor for the structural behavior of the molded part. Important parameters like for example the anisotropy caused by the molding process, internal stresses caused by the process and the position of weld lines are used as the input for the structural solver. A complete simulation chain can look like this – injection molding simulation with Moldex3D followed by the extraction of parameters as described above and a subsequent non-linear structural simulation with MSC Marc. For the coupling the both simulation the Digimat software suite provides a powerful set of tools. Digimat covers several aspects important to set up the simulation chain, like the micromechanical modeling of the non-linear materials and the actual coupling with a non-linear structural solver, and also the mapping of the parameters extracted from the injection molding simulation onto the mash of a structural model.
Structural simulations, especially regarding the simulation of structural failure, can be made arbitrary complicated. In most of the cases it is not necessary to simulate the actual failure – it is often enough to assess the stress and strain state in the loaded model to assess if and where a failure can be expected. This does not mean that the direct failure is not of interest. Although this kind of simulation requires a much higher effort, it can provide a better insight into the susceptibility to failure for the part. This can lead, if considered early, to cost and time reduction later in the development process.
Would you like to know more?
Please contact us: + 49 (0)241-565 276-0 or send us an email to info@simpatec.com .