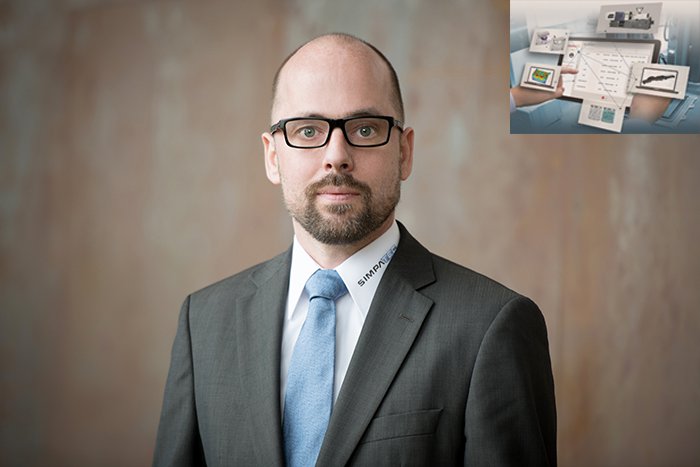
“Talking about the Digitalization of Digitalization”
Interview with SimpaTec's CEO Cristoph Hinse
The SimpaTec Usermeeting 2023 in Nuremberg, Germany, on February 28 and March 1 had practically oriented technical presentations from the circle of Moldex3D users as well as the introduction of product-related new developments on the agenda. Cristoph Hinse, one of the founders of the engineering and software company, had time to answer a few questions after the event.
Traveling to a user meeting as a non-user presupposes a certain tolerance for digital material. Or even a joy in colors - on the "colorful path to the warpage model," as one of the presentations was titled. However, those who expected a rather "nerdy" event faced with topics such as a data management platform for injection molded parts, the modeling of digital twins or the relationship between the creep behavior of polymers and their stress-strain curves, were pleased to discover how close to reality injection molding simulation has become and what a boost in sustainability and efficiency it gives to part development at almost all levels of complexity. What does the pro say?
Kunststoffe: Mr. Hinse, which parts can we confidently produce without a simulation?
Cristoph Hinse: None of them! It’s actually the supposedly simple parts that the simulation has a particularly positive effect on. Mostly with ulterior motive of an easy way to try out something virtually, breaking new ground, comparing different alternatives, and ultimately generating knowledge from conjectures. It is only of secondary importance here whether these assumptions were correct, since even with a supposedly negative result, they are used to decide on the direction to take.
Kunststoffe: At the user meeting, it was repeatedly mentioned how much the quality of the simulation results depends on the quality of the material data.
Hinse: In general, the input data is one of the essential components of the simulation itself. This also includes the material parameters, but not only.
Kunststoffe: How can a user assess this quality? Or what does SimpaTec do to guarantee the quality of the data?
Hinse: Here, Simpatec acts more as a messenger of the information. The data usually derives directly from the material manufacturer. For some years, they have to some extend also been determined in the in-house lab of Coretech, the developer of Moldex3D. There is a lot of information here that the user has direct access to: on the one hand, every data record is completely transparent, which means that every user is given source information for each component. On the other hand, the time that the characteristic values were determined is also stored in each data record ...
... curious how it will continue!!! The complete interview can be read and downloaded here😊